Cracking the code on maritime carbon capture
How Seabound developed a simpler, cheaper technology to reduce emissions from shipping today.
By: Alisha Fredriksson, Co-founder and CEO at Seabound
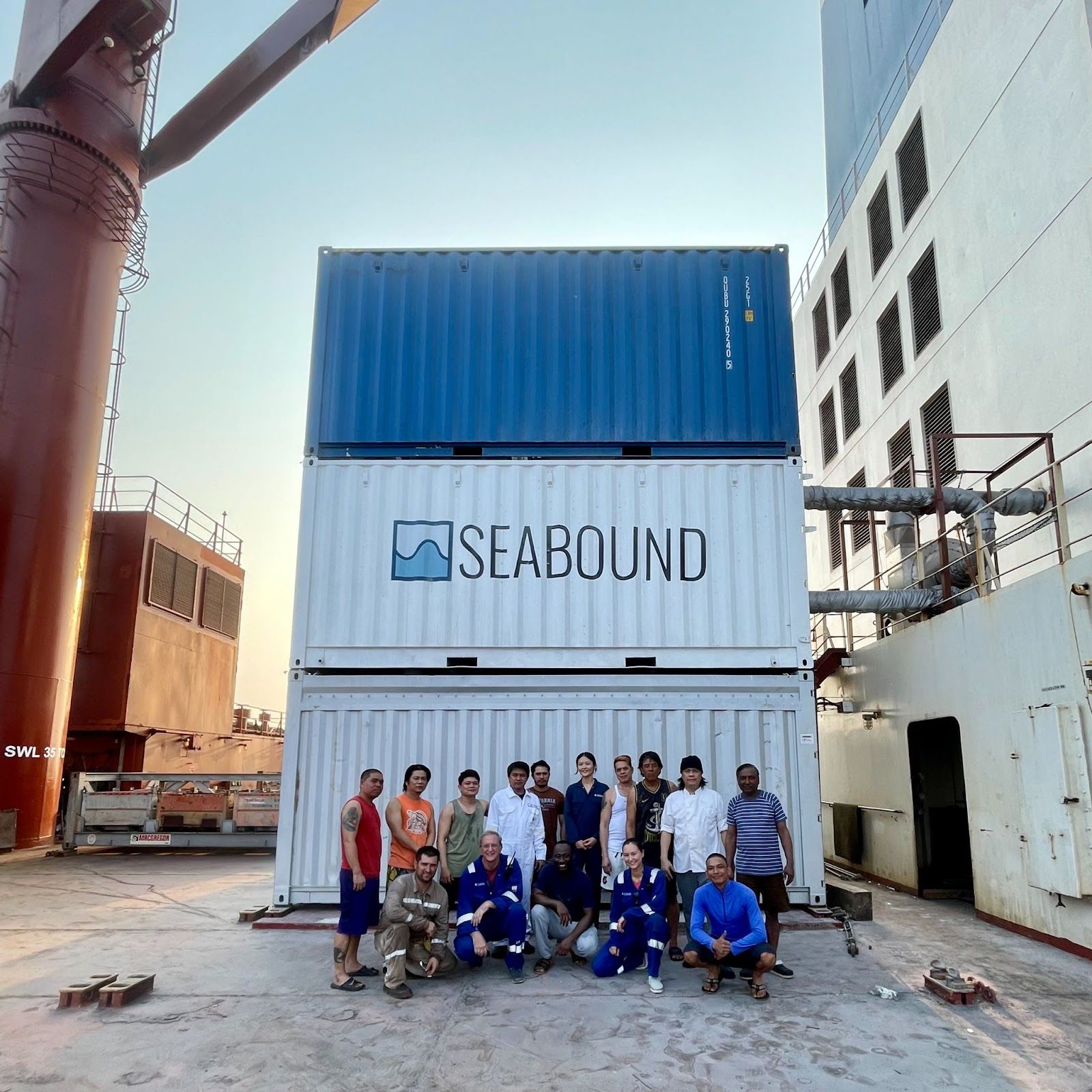
Table of Contents
- Simpler carbon capture, made for ships.
- The tech that makes it work? Chalk.
- The proof is in the pilot.
- Calling prospective anchor partners.
As any shipowner anxious about new emissions regulations knows, shipping is one of the final “hard-to-abate” industries without ready decarbonization solutions. With clean fuels still decades away and efficiency solutions woefully inadequate, the answer is onboard carbon capture for ships. But no one’s been able to crack it — until now. At Seabound, we’ve developed a new approach to make maritime carbon capture work at scale — simply and cheaply. And now we’ve got the real world results to prove it. We’re thrilled to announce the first successful pilot of our carbon capture tech onboard a seagoing vessel. With this world first, shipping is about to get a whole lot cleaner.
Simpler carbon capture, made for ships.
Before we dive into the results, let me explain how our carbon capture is different — and why it matters. Past attempts at maritime carbon capture struggled because they tried to take a technology made for large, land-based CO2 emitters (e.g. power plants or heavy industry) and miniaturize it for smaller, moving ships. This approach was riddled with problems: High capital expenditure (up to $30M in CAPEX), difficult space requirements, high onboard energy consumption, difficulty offloading pure CO2 at ports.
To really clean up shipping, we had to figure out a carbon capture system for ships that was purpose-built for ships. And purpose-built for customers keen to install and deploy it ASAP.
First, we took a long look at the process. Typically, carbon capture has three steps:
Capture - CO2 is bound to a binding agent e.g. a sorbent or solvent
Regeneration - CO2 is separated from that binding agent, resulting in pure gaseous CO2
Liquefaction - gaseous CO2 is put under high pressure and low temperature to be compressed and liquefied
The second step - regeneration - requires the most complicated and expensive equipment, and the second and third steps are the most energy-intensive.
What if we could simplify it? Could there be a workaround to transferring these components to ships? That’s when we had our a-ha moment: Decouple the carbon capture process. We realized that to make carbon capture work on ships, we only had to capture the CO2 onboard. We could save regeneration and liquefaction for land.
In doing so, we could minimize equipment onboard to reduce capital expenditure and prohibitive space requirements.
We could also build fewer, larger regeneration facilities nearby key ports to service many ships arriving with captured carbon. (This would have the added benefit of leveraging economies of scale to further reduce equipment CAPEX and utilize land-based energy to avoid consuming extra energy onboard.)
And we could keep CO2 locked in its binding agent to prevent the need for pure liquid CO2 discharging facilities in ports, thus dramatically increasing the scalability of the solution.
This decoupling insight was hugely exciting for me and my co-founder, Roujia Wen. Now all we needed was the right tech.
The tech that makes it work? Chalk.
Through extensive research, we came across a second-generation type of carbon capture technology called calcium looping that facilitates this decoupled approach. Calcium looping involves chemically reacting CO2 (e.g. in ships’ exhaust gas) with calcium oxide to create calcium carbonate, an inert, non-toxic material that is solid at ambient temperatures. In other words: we’re turning CO2 into chalk.
Fortuitously, we found a world-renowned researcher in calcium looping who had reached the same conclusion about the merits of decoupling carbon capture from regeneration and liquefaction. He was developing a novel, compact form of calcium looping device, which we realized could be uniquely promising for ship space constraints, and so together we decided to co-develop the technology for the maritime sector.
This compact calcium looping tech has another key advantage for the shipping industry: it captures sulphur emissions at an even higher rate than CO2, which means that it can be used as a dual-purpose scrubber and carbon capture system.
The proof is in the pilot.
Now for those results I promised.
After a series of land-based prototypes and trials, we recently completed our first pilot onboard a container ship, capturing carbon at ~80% efficiency and sulphur at ~90% efficiency.
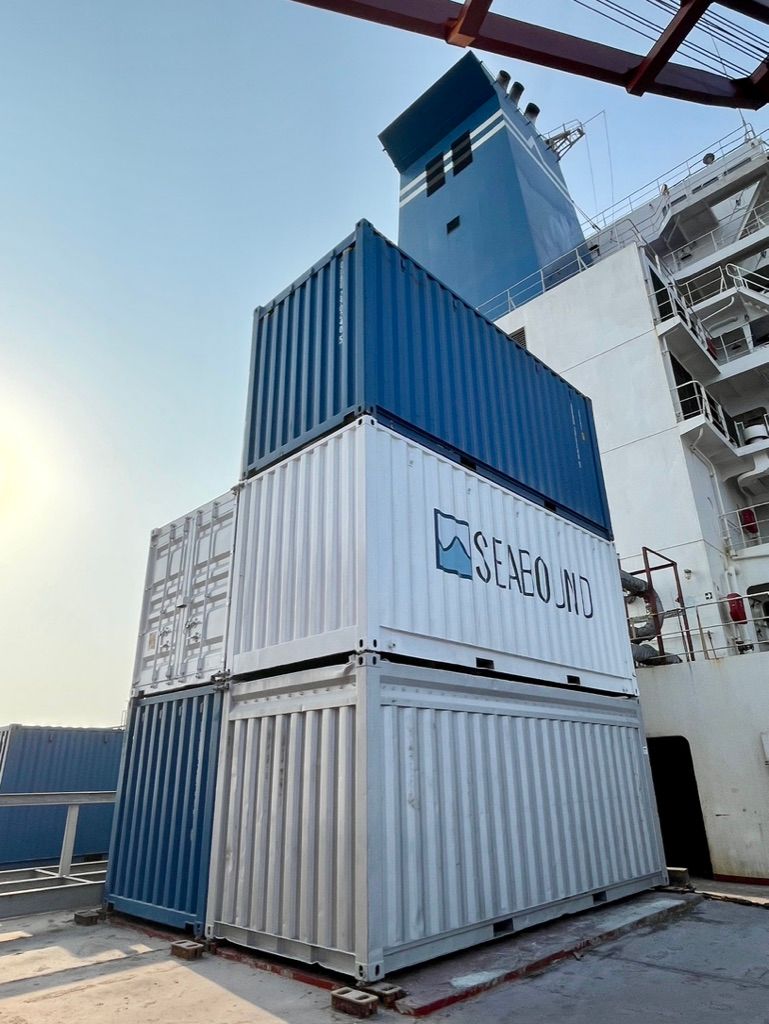
The goal of Pilot Ship #1 was to install Seabound’s novel carbon capture system onboard a commercial vessel to test its functionality with a marine engine and in a marine environment.
With an aim to rapidly and iteratively de-risk our technology, we temporarily installed a Seabound prototype onboard a 3200 TEU container ship called Sounion Trader, thereby transforming her into a ship-shaped lab.
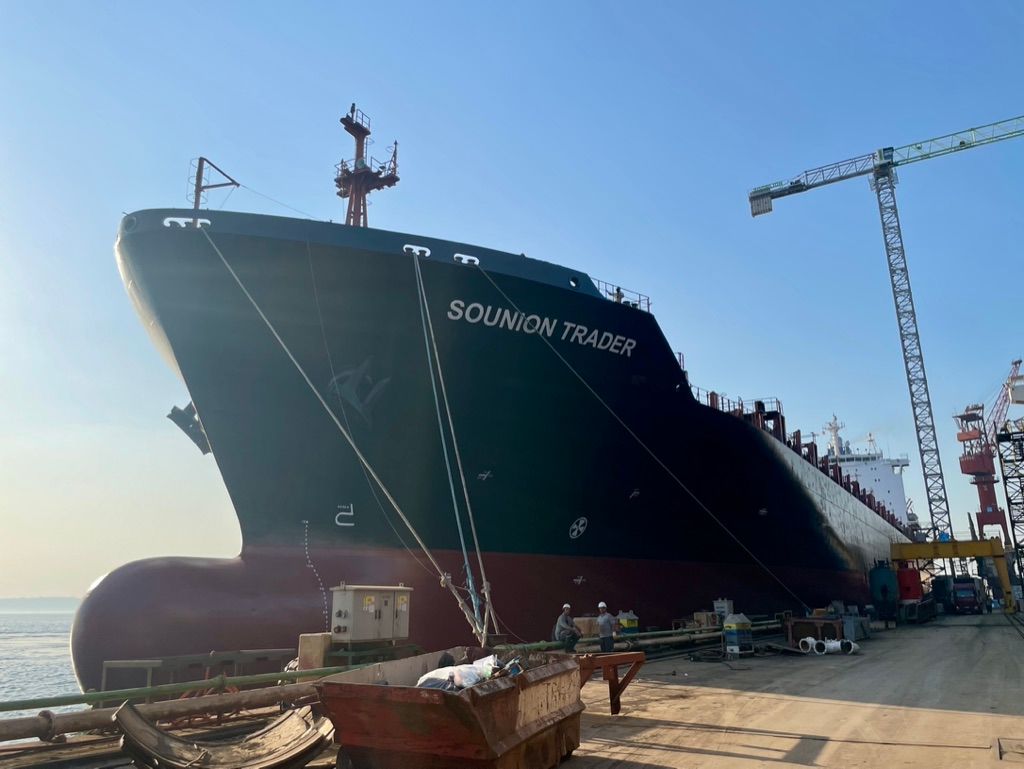
To complete the installation, we moved the Seabound team to a shipyard in Yalova, Turkey, where the Sounion Trader was undergoing routine maintenance. Over the course of several weeks, we collaborated with the shipyard and the ship’s crew to install our equipment and connect it to one of the ship’s auxiliary engines. We also worked with the American Bureau of Shipping and Lloyd’s Register to gain approval for operating the system onboard and to conduct a detailed risk assessment, respectively. When the ship set sail for the Middle East, we joined the crew for two months, taking turns to run numerous carbon capture trials and gain hands-on experience operating at sea. With each test, we managed to increase the carbon capture rate, culminating in 78% efficiency and ~1 ton of CO2 captured per day.

The exciting results of Pilot Ship #1 prove that we can effectively install and operate Seabound’s compact calcium looping device in a commercial marine environment. While this prototype was relatively small given the size of the ship, it crucially unlocks the next, larger-scale systems.
We’re grateful to our first customer, Lomar Shipping, and their innovation arm, lomarlabs, who provided both the vessel and invaluable expertise to facilitate the pilot. Thank you also to Hapag-Lloyd for supporting the project while chartering the vessel and to the UK Government for providing £1.2M in grant funding via Innovate UK and the Clean Maritime Demonstration Competition - Round 3.
Calling prospective anchor partners.
So what’s next for Seabound? We’ve already designed and built a new-and-improved iteration of our carbon capture system that leverages the learnings from Pilot Ship #1. We’re currently testing this at our workshop in London before we scale up the system to capture 50 tons of CO2 per day.
In bigger news, we plan to deliver the first commercial Seabound systems in 2025 and are now signing up pre-orders with shipowners and customers around the world.
Our ambition is to capture carbon onboard 1000 ships by 2030 to make a rapid and meaningful dent in tackling the climate crisis.
To pioneering shipowners who want to lead the industry’s transition: you can reduce emissions from your existing fleet today and no longer need to wait for clean fuels. We’re just getting started to accelerate maritime decarbonization and hope you’ll join us in this journey.
To catch a behind-the-scenes view of this first pilot, check out the mini documentary below.
Related
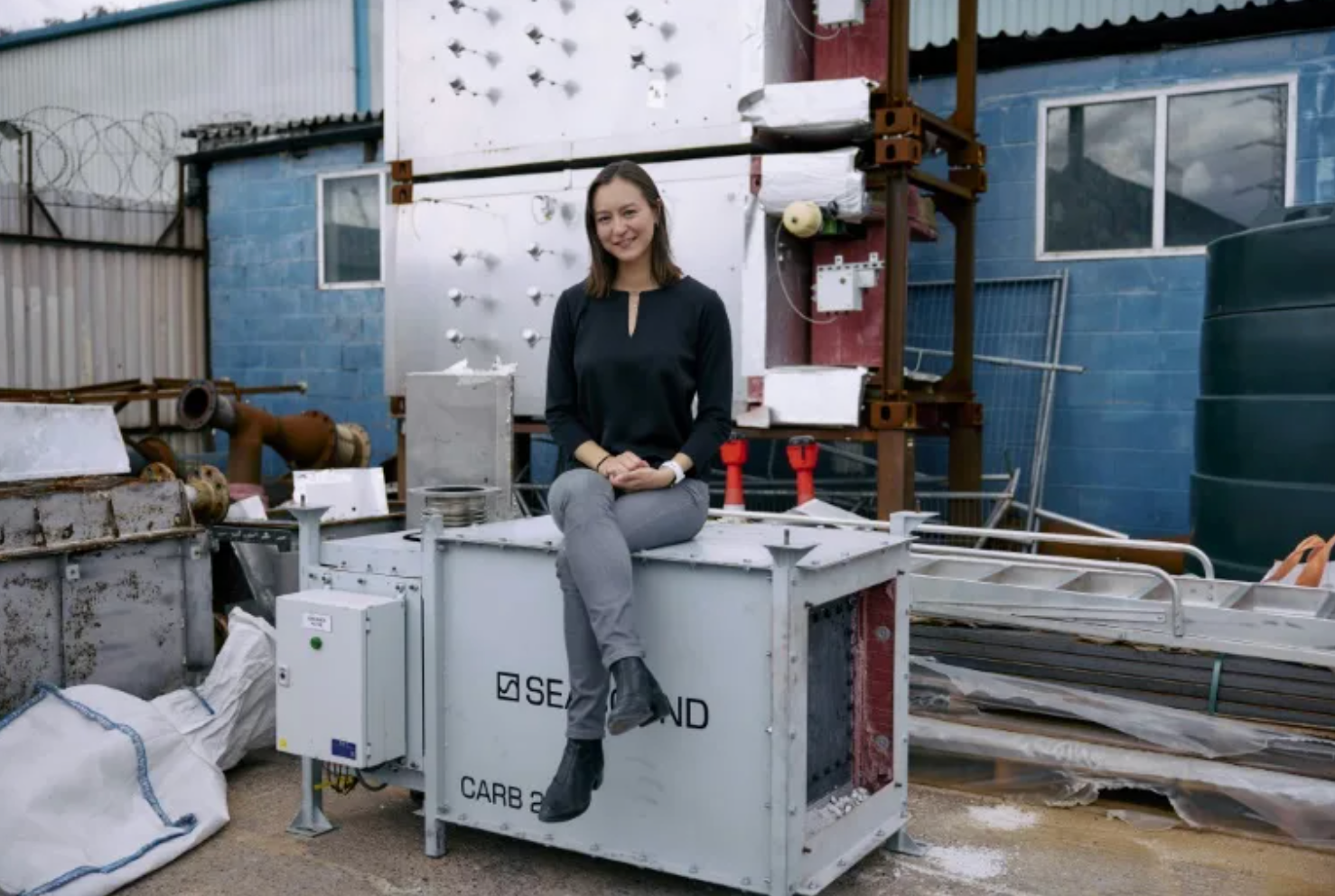
Yahoo News: UK startup looks to cut shipping's carbon emissions
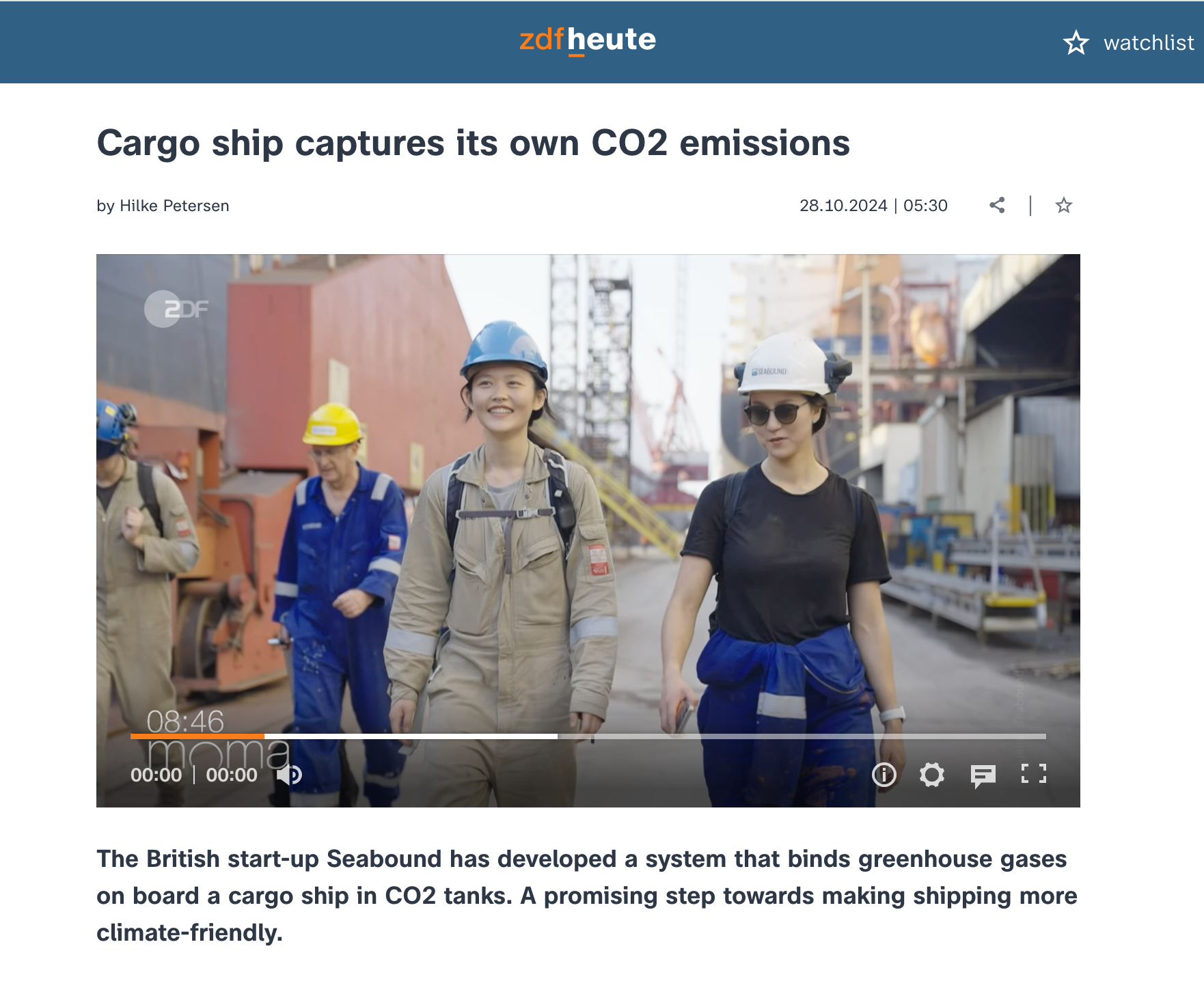
ZDF: Cargo ship captures its own CO2 emissions
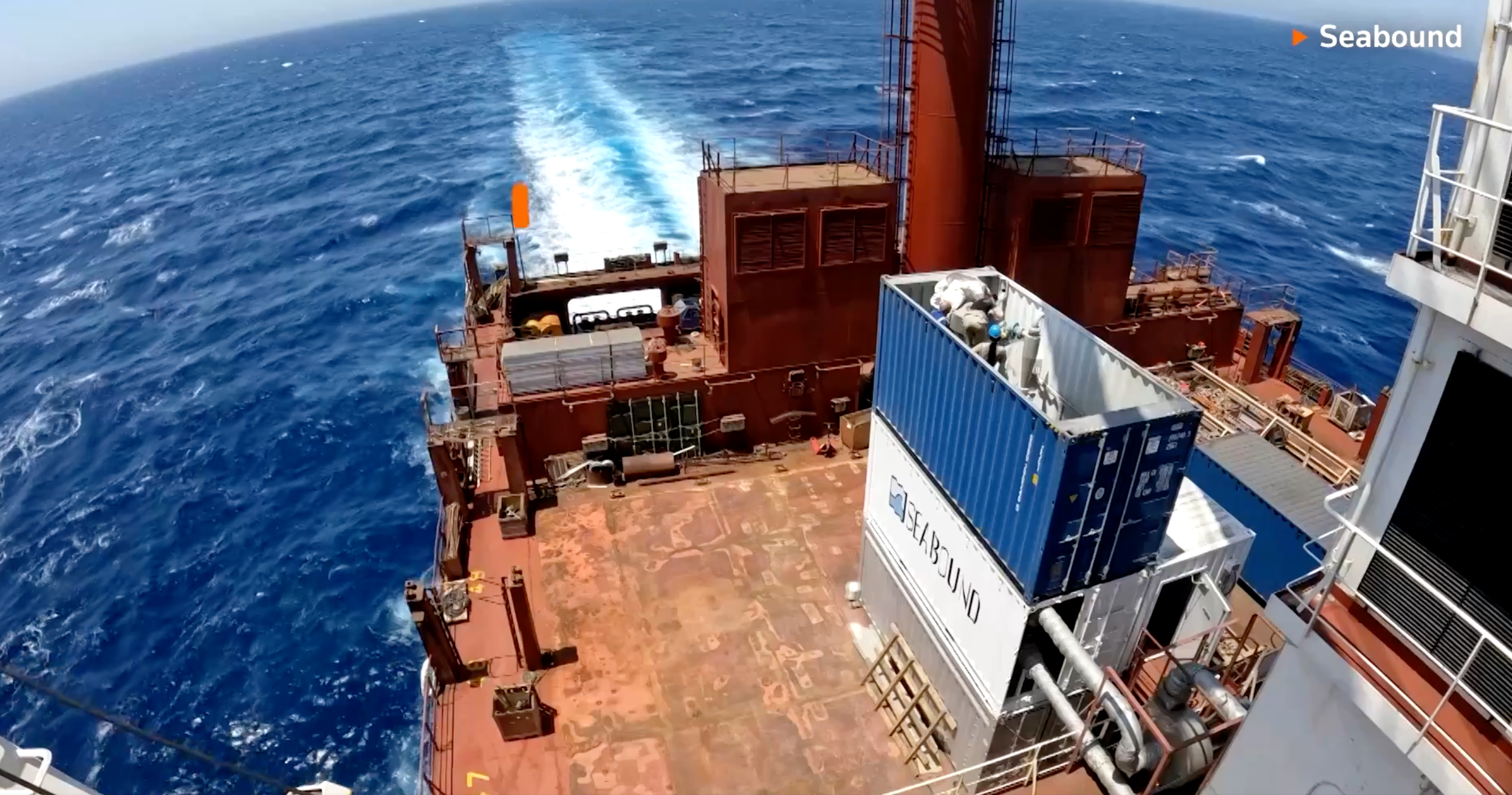
New Scientist: A container ship just tested a system to capture its own CO2 emissions
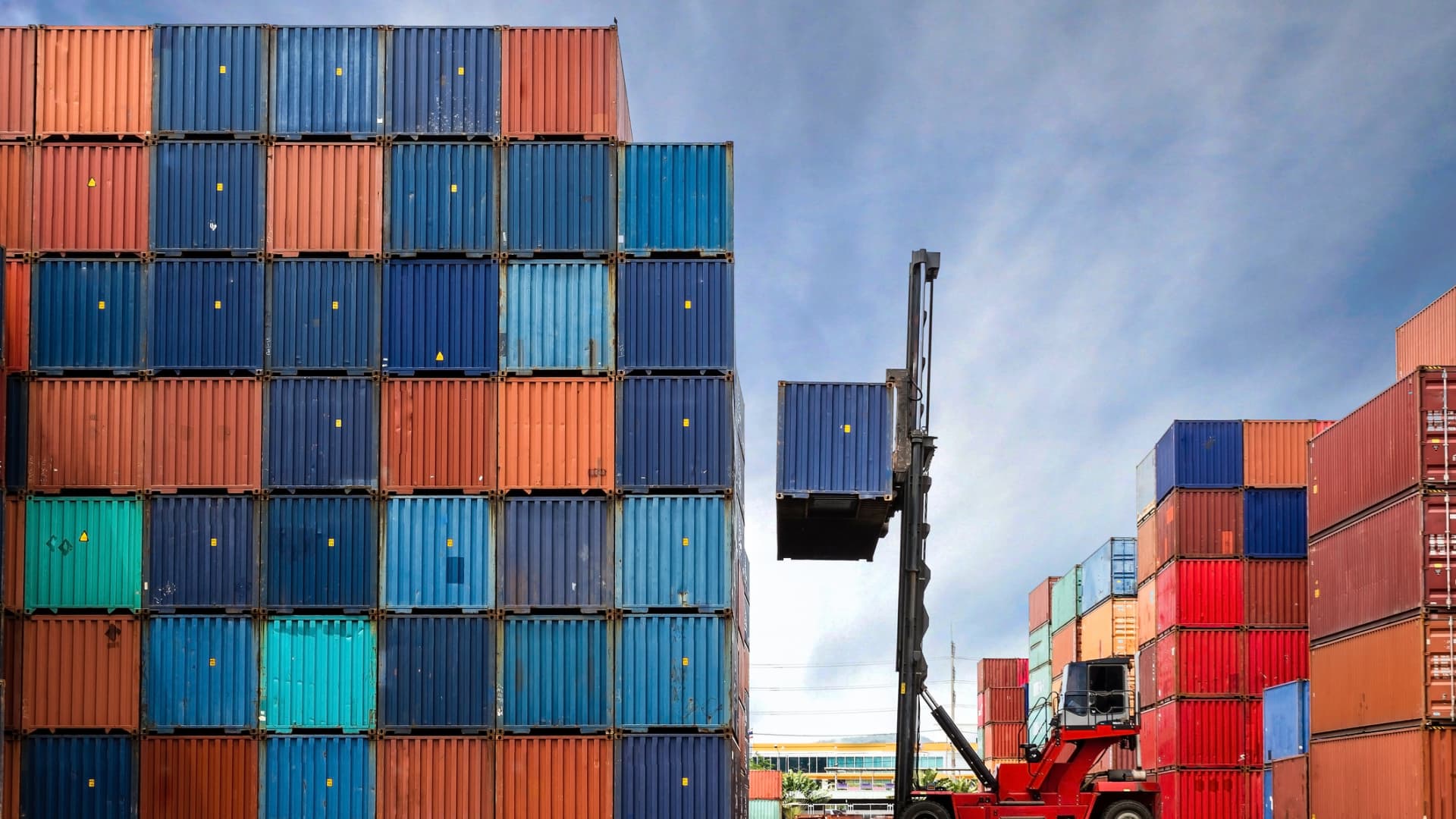
Ship Technology: Seabound partners with Lomarlabs to develop carbon reduction tech
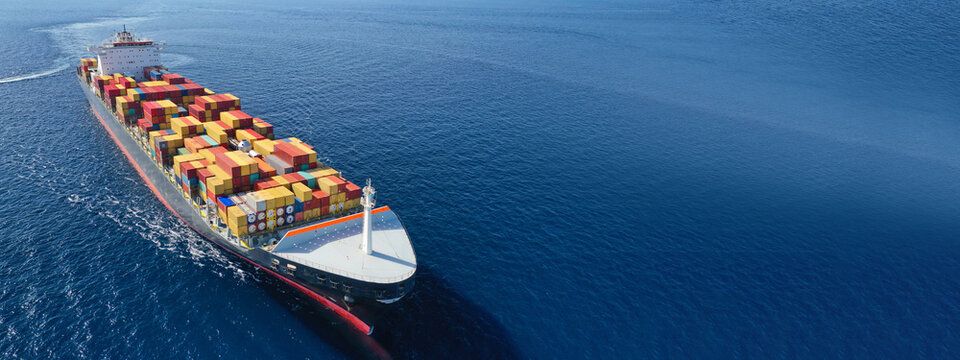
The Engineer: lomarlabs teams up with Seabound on maritime decarbonisation
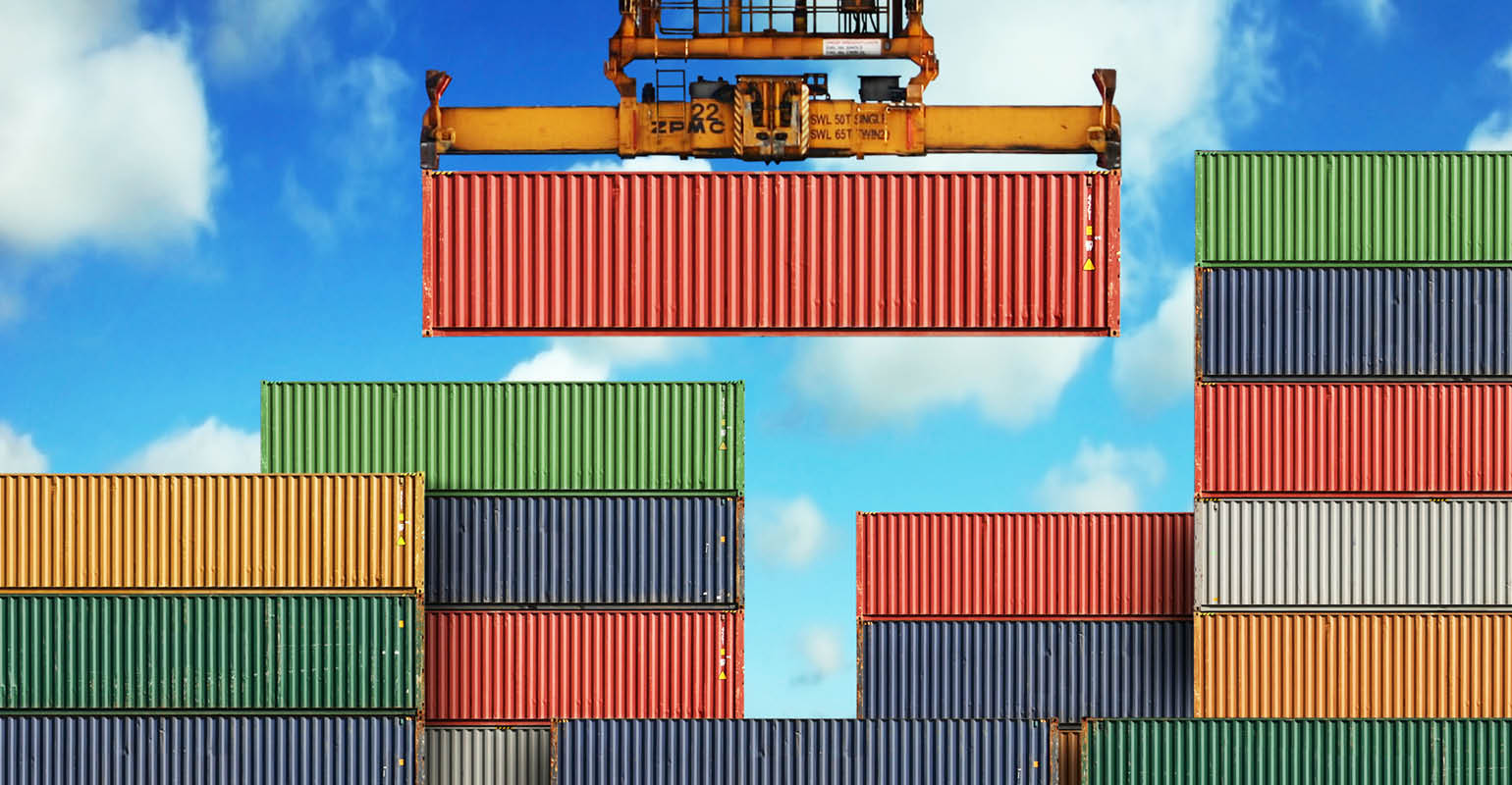
Energy Institute: Can carbon capture get ship shape?

Carbon Herald: Lomar Partners With Seabound For CO2 Capture On Vessels
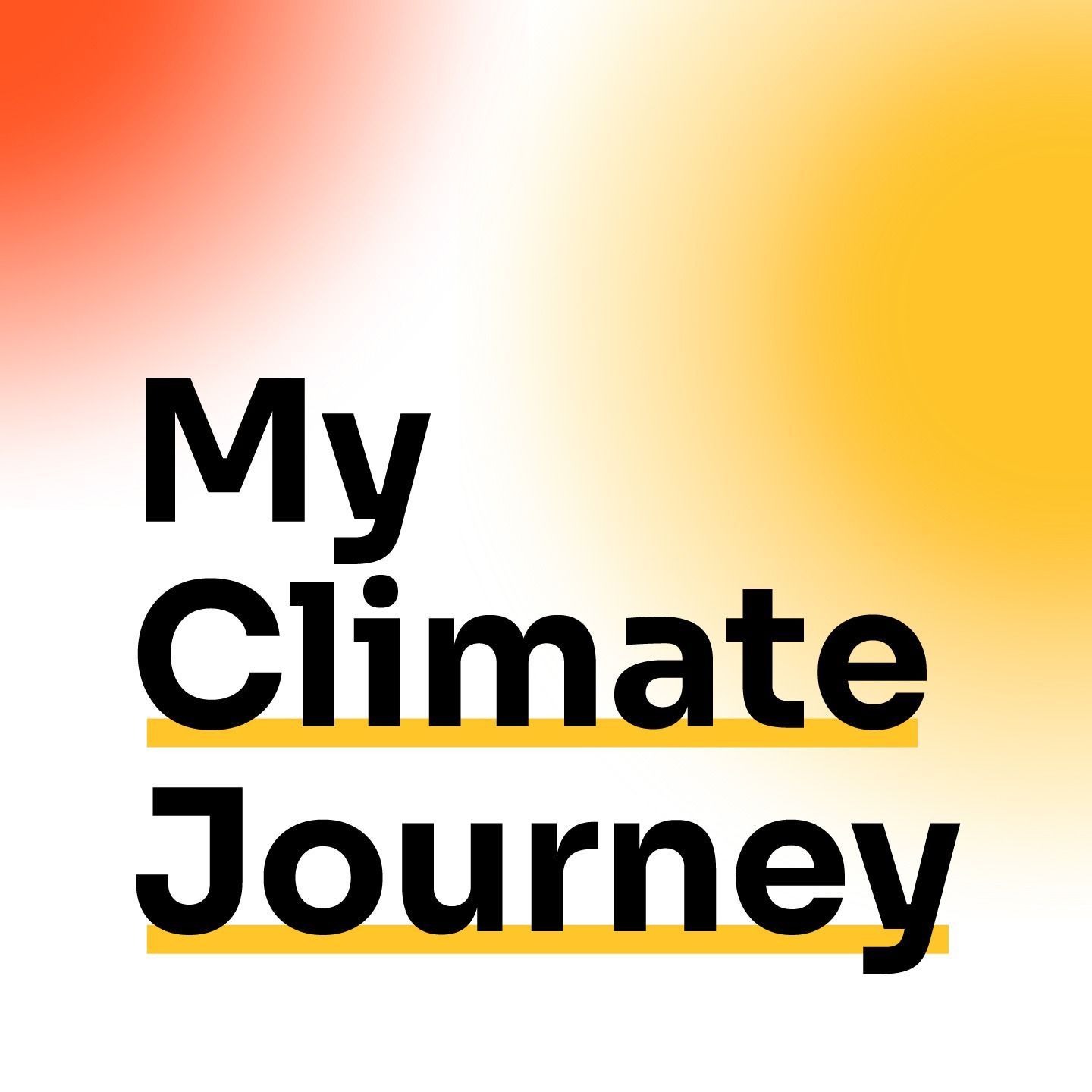
My Climate Journey: Startup Series Seabound